【技术特点】
针对有色冶炼烟气洗涤污酸废水重金属浓度波动大、重金属形态复杂及酸度高等特点,研发了“选择性吸附-气液强化硫化-酸浓缩-氟氯分离”的新工艺,以实现污酸中有价金属和硫酸等有用资源的高效回收及砷和氟氯等有毒有害元素的高效开路。通过选择性吸附可以实现污酸中稀散金属铼、硒等的高效回收;通过气液强化梯级硫化对污酸中的铜、铅、镉等有价金属实现分步回收,得到的硫化渣中重金属品位在50%以上,可作为硫精矿回收有价金属,同时实现污酸中的砷的单独开路,有价金属与砷的分离率在98%以上。结合选择性电渗析技术、蒸发浓缩技术、氟氯分离技术,对污酸中的酸浓缩至50%以上回用,酸的回收率可到90%以上,氟氯离子实现高效分离,分离率可达99%以上。污酸废水通过新技术处理后,无需石灰中和,避免大量中和渣的产生,渣量不到传统方法的8%。实现了有价金属和砷的分离,避免了砷在系统中的循环富集,净化水全部回用,实现污酸废水零排放。
【技术应用】
新技术已通过有色金属工业协会组织的科技鉴定,院士专家组一致认为该技术居国际领先水平,获2016年度有色金属工业学会科技发明一等奖。目前该新技术已建立了可移动式“高浓度重金属废水资源化利用与回收系统”,在全国10多家企业大型有色企业现场完成了扩试和工业化试验,在紫金铜业有限公司成功建成了处理规模为500m3/d的示范工程。
原紫金污酸废水采用“硫化钠硫化+铁盐+石灰中和”处理工艺,原工艺处理硫化钠投加量大,砷滤饼产生量大,且传统硫化处理后残余的砷浓度高,对后续中和处理冲击负荷大,导致系统出水不稳定。
采用新的气液强化硫化技术,相比原硫化钠硫化工艺,每年可节约硫化钠用量约800吨,每年可减少砷滤饼的产生量约为1000吨,年节约运行成本1000万元。
紫金铜业公司现场照片
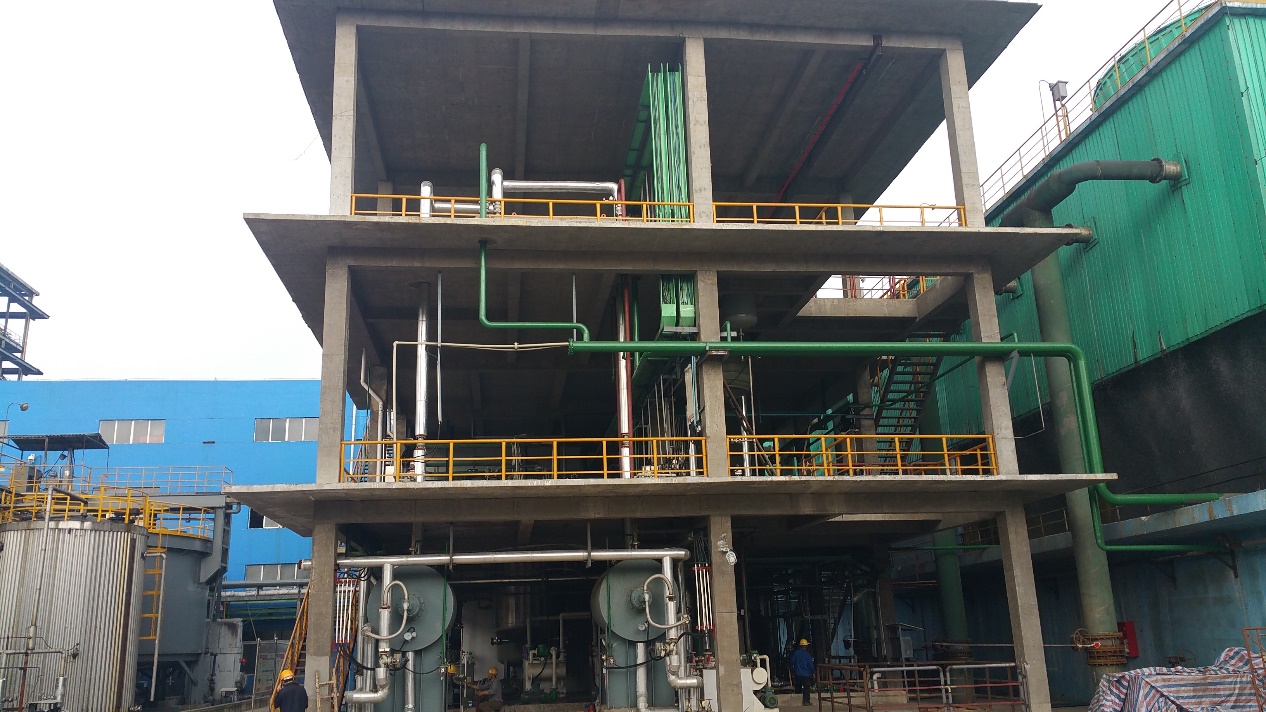
硫化反应整个系统
反应系统
污酸循环与输送系统
污酸气液强化硫化全自动控制系统